"This year, our company name was renamed by Hyun Shuo Optoelectronics, which means that we will strategically develop from professional equipment to intelligent manufacturing equipment." He said at the 15th Gaogong LED Industry Summit Forum.
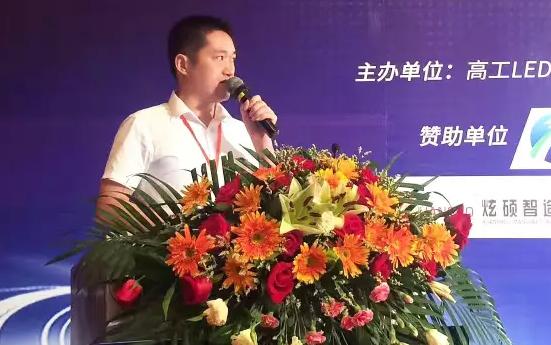
Hyun Shuozhi, the director of the division of the optical division, Tao Dahu
In the past two years, the state has been advocating the manufacture of Industry 4.0 and 2025. For LED companies, how to promote the development of industrial industry 4.0 and 2025 is worthy of consideration. In this regard, Hyun Shuo Zhi made a joint discussion with several listed companies, how to save labor and bring direct economic benefits to the company?
According to Tao Dahu, “Talking about smart factories, Hyun Shuozhi is also at the stage of exploration. In the future, we will continue to optimize software and hardware for smart factories. In addition, we will follow the valuable suggestions of customers and jointly promote the healthy development of smart factories. ."
So, why do you want to be a smart factory?
As we all know, almost every enterprise is facing many pressures such as increased employee management costs, difficulty in recruiting workers, improved product quality requirements, rising wages, and insufficient plant area. It is difficult for companies to guarantee lucrative gross profit and net profit. As the cost of equipment continues to decline, the era of automation and intelligence is ushered in.
“At present, we are constantly optimizing in space intelligence, and we have created a professional team for this purpose. For smart factories, we already have a complete solution, and this solution must be implemented this year to solve more problems for customers. Practical problems." Tao Dahu said.
Hyun Shuozhi's solution can realize the robot instead of manual in the front part of the package, specifically: solid crystal segment - solid crystal segment manipulator - wire segment - wire segment robot - dispensing segment - baking segment.
Up to now, the total capacity of this production line per day = 28 sets of solid crystal machine X (24K / H) X22 hours = 14.784K = 1026 boxes, wire bonding machine by capacity ratio: 28 sets of solid crystal machine (single 24K / H ), 56 wire bonding machines (single 12K/H), 3 tunnel furnaces, 28 dispensing machines (single 24K/H), 2 plasma cleaning machines, 22 robots (16 sets of Longmen group + transportation materials) 6 units).
Tao Dahu proposed that we should make full use of all the equipment, and not waste any process, manipulator, oven, etc., and get an optimized number of machines.
If it is calculated according to the calculation of 22 hours per day, a total of 14.8 KK is produced, and the company's regular production requires a total of 94 people, and this planned production line only needs 40 people. A total of 54 people were saved, saving 57.5%.
According to the annual salary, welfare, subsidy, bonus, etc. per person per year, the savings of 50,000/year can save 2.7 million/year; 46 ovens can be saved, the average price of each oven is 0.6 million, saving a total of 276,000; saving half of management staff 6 People, the average wage benefit of 10 / year, can save 600,000 / year.
It is undeniable that the entire intelligent factory process realizes advanced technologies such as network of production equipment, visualization of production data, paperless production documents, transparent production process, and unmanned production site. Through the various information sensors of the device, real-time collection of any object information that needs to be monitored, connected, and interacted. Achieve intelligent, interactive, seamless connectivity between people, devices, and systems.
At the production site, data is collected every few seconds through barcodes, sensors, PLC control systems, industrial Internet, etc., and data is used to analyze equipment startup rate, operating rate, failure rate, productivity and other information. Once a process fails, an alarm is generated, and the big data technology is used to find the cause of the failure, which is convenient for solving the problem.
In addition, the smart factory can build a green smart system, and the production documents are paperless. The staff can quickly query, browse and download the required production information on the spot. The data generated during the production process can be archived and saved in time.
Enterprises can also wirelessly monitor production, task compliance, quality clearance and other information through mobile phones. In terms of safety, the entire production line will be protected by a cover. The door cover is equipped with an inductive switch. When a person enters the door panel, the anti-stall plate will automatically fall to ensure the safety of personnel.

Servo Systems,Servo Drive System,Servo Positioning Systems,Cnc Machine Ac Servo
Zhejiang Synmot Electrical Technology Co., Ltd , https://www.synmot-electrical.com